Introduction: Aim of any dental treatment is to replace structure as well as function of the damaged or lost teeth. Among the various categories of dental treatments, in the recent past dental implant become the most popular dental treatment modality. However, beside the issue of faster osseointegration, screw loosening and component fracture are also main concern of contemperory dental implants. So in the present study, simulation of fatigue testing as well as experimental fatigue testing of inhouse developed dental implant is done to compare their results as well as to validate the design of inhouse developed implant system as per ISO Standard [1].
Materials and Methods: Fatigue test experiments are carried out on the Bose Electroforce® machine with the test geometry setup as shown in Figure 1. The static compression load experiments are carried out to find the load to failure for the same test geometry as in the fatigue test. For the fatigue testing, implants are tested at 14 Hz loading frequency with load magnitudes varying as 40, 50, 60, 70 and 80 percent of the static load value.
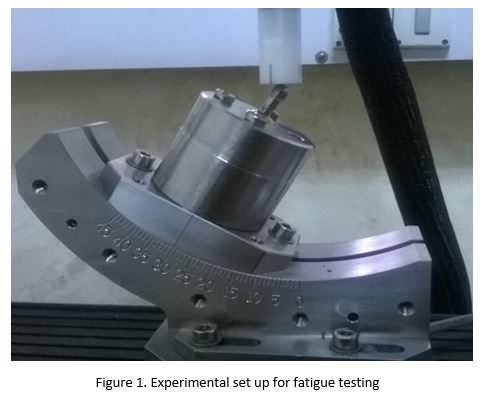
The geometric model of the implant system is assembled using SolidWorks™ software. To mimic the test experiment set up, the implant is mounted on a test fixture with a surface inclined at 30 degrees to the horizontal surface. Then the model is imported into ANSYS Workbench environment for carrying out the simulation (figure 2.).
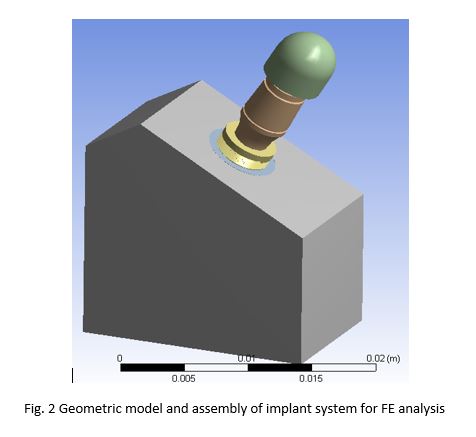
Results: The average static load value is 308 N ± 23.52 N.
The implant system survived five million cycles at 40 percent of the static load, i.e. fatigue loading of 124 N and 12.4 N, at a loading frequency of 14 Hz.
Simulation predicts failure in the implant system at 350 N approx and the failure is predicted in the hex region of the abutment.
Discussion: The implant system survived five million cycles at the fatigue load limits of 124 and 12.4 N thus qualifying the ISO 14801 standard of testing the reliability of a dental implant. It is discovered that with decrease in magnitude of fatigue load, from 50 to 40 percent of static, the implant system life increases drastically from 0.1 million approximately to five million.
Conclusion: Load values for mastication of routine food products are reported to be in range of 70-150 N therefore this implant system can be potentially successful for replacement of teeth [2].Further there is similar trend of failure in experimental set up as well as in FE simulation.
Council of Scientific and Industrial Research (CSIR)
References:
[1] ISO 14801:2007: Dentistry-Implants-Dynamic fatigue test for endosseus dental implants
[2] Scully, C., 2002, Oxford Handbook of Applied Dental Sciences, Oxford University Press –ISBN 978-0-19-851096-3 P156